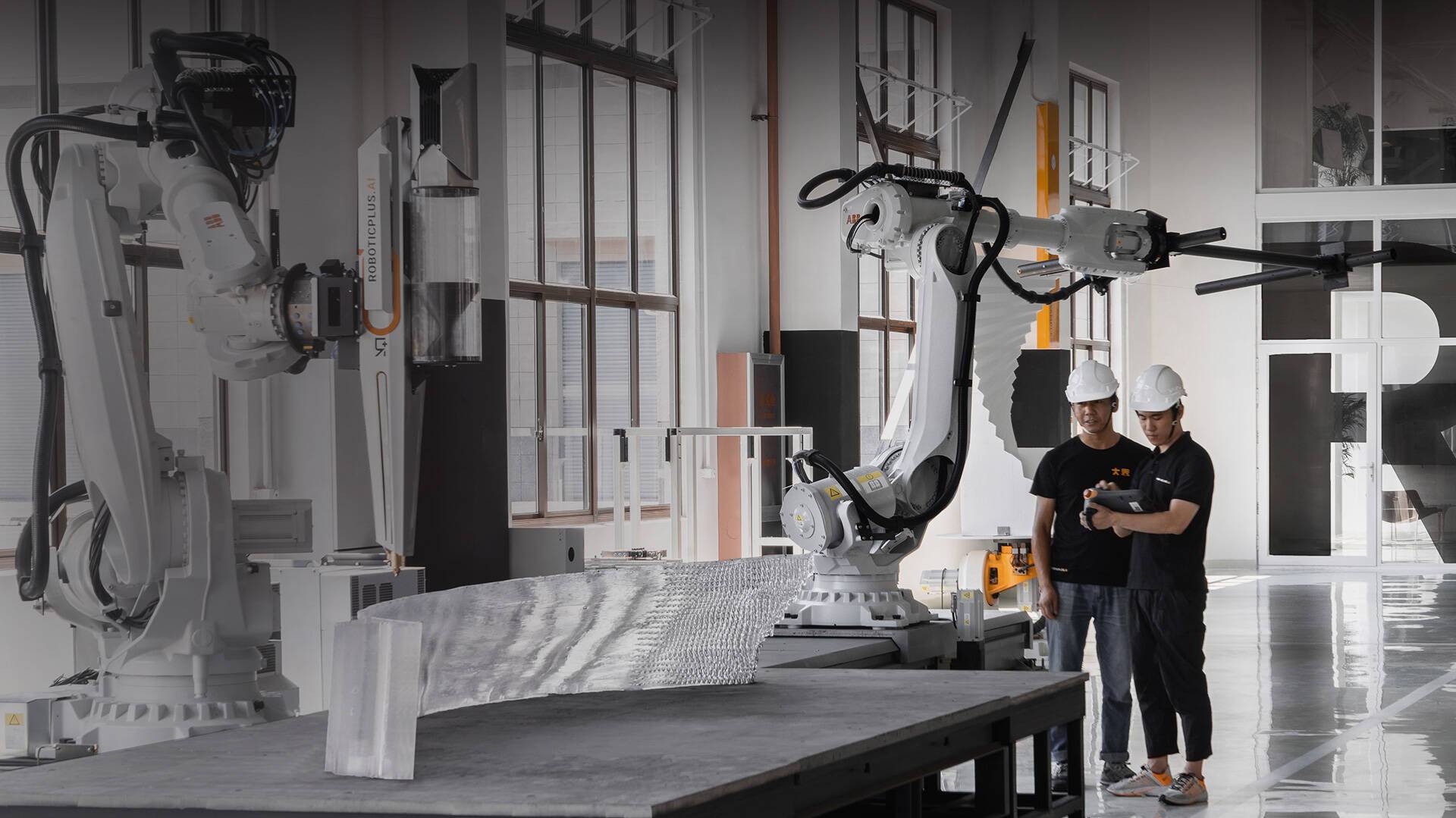
News
cutting-edge technology
Shenzhen Roboticplus.AI Intelligent Manufacturing Technology Co., Ltd., rooted in the South China region, is a subsidiary of Shanghai Roboticplus.AI Robot Technology Co., Ltd. The company is committed to promoting the development of prefabricated construction industry.
This post introduces the "Modular Steel Structure Robot Production Line and Implementation Cases for Order-based Manufacturing." In the future, "Shenzhen GrandRealm" will also regularly share flexible smart manufacturing solutions for Modular Integrated Construction (MiC).
On October 13, 2021, the Hong Kong Special Administrative Region government unveiled the "North Metropolis Development Strategy," which transcends administrative boundaries between Hong Kong and Shenzhen in spatial concepts and strategic thinking. Hong Kong will use the "North Metropolis Development Strategy" as a long-term plan to initiate the planning and construction of the North Metropolis, undoubtedly ushering in a new chapter in the economic and social development of Hong Kong. The plan aims to accommodate over 900,000 residential units, accommodating an estimated population of 2.5 million. Additionally, in the 2022 Policy Address, the government introduced the concept of "Simplex Homes" to encourage fast construction using standardized and simple designs, as well as "assembled synthesis." The modular construction market still holds significant potential for development.
However, the automation and intelligent development in the construction industry have been slower compared to manufacturing industries such as automobiles and electronics, and the field of modular construction is no exception. Currently, many components in modular factories are still manually constructed using traditional methods. In light of the latest development goals for the Greater Bay Area and in line with the requirements of national high-quality development, the modular construction industry is gradually improving from a technological, standardization, and regulatory standpoint. The trend towards intelligent solutions is becoming increasingly evident. With the explosive growth of the modular construction market in recent years, the entire industry faces both the pressure and impetus to undergo industrial intelligent upgrading. Thus, leveraging intelligent construction technology to reduce costs and increase efficiency has become a major focus of attention within the industry.
Shenzhen Roboticplus.AI, deeply rooted in the South China region, adheres to an independent research and development approach. They have developed the RobimWeld software based on welding technology and, in response to the needs of the modular construction market, have proposed a GrandRealm modular steel structure robot production line, specifically oriented towards order-based manufacturing.
Market challenges
1.Diversified market orders and product uncertainties
Over the years, the construction industry has pursued design diversification, resulting in a wide range of personalized demands. Although the introduction of standardization and productization concepts in modular construction has brought relative control over product diversity, there are still different product types emerging based on project types and site conditions. The standardization level in modular construction remains significantly different from other traditional industries, such as automobiles and electronics. Finding a balance between customized production and large-scale automated production, while enhancing production line flexibility, presents a major challenge within the industry.
Product diversification © AluHouse
2.Low automation level in the production process
In recent years, with the nation's strong focus on developing intelligent construction technology in the building industry, some companies have taken the lead in adopting advanced automated production lines for smart upgrading. However, the overall automation rate in the industry remains relatively low, and many welding processes still heavily rely on manual operations. Compounded with the society facing an aging population problem, the average age of production workers is also increasing gradually. The low automation rate may lead to insufficient production capacity in the future due to labor shortages.
3.Unstable manual welding quality
In traditional welding processes, the inconsistency of manual operations results in an inability to ensure reliable welding quality. Additionally, the welding speed may also vary, leading to unstable weld seam quality, substandard welding strength, and even affecting the overall performance of the components.
4.Inefficiency of traditional workpiece processing methods
In the traditional production process, workers need to frequently adjust fixed fixture positions, and the imprecise positioning method may result in insufficient precision of the workpiece. Moreover, a significant amount of time is involved in reading drawings, measurements, marking, and adjustments. The workers' productivity and accuracy in producing the workpiece can be influenced by information dissemination, the work environment, and their personal mood, leading to reduced efficiency and accuracy in workpiece production.
Roboticplus.AI Self-developed Innovative Technologies
1.Optimization of Prefabricated Steel Structure Production Process and Implementation of Intelligent Welding
The independently developed intelligent welding system is equipped with cutting-edge geometric algorithms, visual algorithms, robot motion control algorithms, and other technologies. It can rapidly read steel structure models, utilize various types of visual sensors for positioning and correction, and optimize the production process of prefabricated steel structures. The system can automatically generate matching welding paths and motion postures, enabling one-click activation and intelligent welding. This technology significantly reduces the need for traditional processes such as dimension marking and verification, thereby shortening the delivery cycle.
2.Laser Vision Algorithm for Precise Weld Seam Localization
The laser vision algorithm enables fast scanning of the workpiece, accurately identifying the position of the weld seam, and autonomously handling any deviations. This technology avoids welding position discrepancies caused by inaccurate materials from preceding processes. Additionally, the algorithm exhibits strong adaptability to various environmental conditions, eliminating limitations on welding precision and quality resulting from harsh factors such as environmental light, arc glare, and smoke during manual operations.
3.Intelligent Welding Process Expert Database Covering Common Welding Applications
The intelligent welding process expert database encompasses various welding application types, including welding materials, shielding gases, welding joint configurations, basic shapes and dimensions of weld seams, and spatial orientations of weld seams. Integrating with an intelligent data decision-making system, this process expert database can provide the most suitable welding process configurations based on known data information, such as current, voltage, welding speed, welding gun angle, oscillation amplitude and frequency, gun movement method, arc ignition and termination, and joint parameters. This overall enhancement in efficiency ensures welding quality stability and consistency.
4.Multi-robot Collaborative Motion Control Algorithm
The robot motion control algorithm incorporates collision detection and intelligent trajectory planning capabilities, ensuring comprehensive consideration of process, efficiency, and safety. When dealing with complex welding tasks, it can rapidly identify the positional relationships between the robot body, components, and the environment, thereby avoiding occurrences of robot collisions, limits, singularities, and other undesirable situations during actual welding. Additionally, the algorithm intelligently plans processing trajectories and welding process orientations, saving costs on manual debugging and enhancing robot operational efficiency.
Roboticplus.AI X AluHouse
Roboticplus.AI has entered into a collaboration withAluHouse, a global leader in modular integrated construction. Leveraging the prefabricated steel structure construction market in the Greater Bay Area, they have designed an efficient and flexible welding production line that allows for adaptable and intelligent production solutions. This pioneering production line represents an industry-first, and through its implementation and practice, it marks a significant step towards the emerging era of industrial intelligent construction for the modular integrated construction industry.
The project incorporates Roboticplus.AI flexible production system, specifically developed for the MiC (Modular Integrated Construction) industry. By introducing automated welding robots, flexible fixtures, laser vision recognition systems, and GrandRealm's proprietary RobimWeld software, the production efficiency and consistency of the MiC components are significantly improved. The system is capable of handling workpieces with dimensions of approximately 4-12m in length, 3-3.5m in width, and 0.1-0.2m in thickness, maximizing compatibility with various MiC product specifications. It is designed to meet the production demands of diverse products in the future, including transitional housing, simplex homes, data centers, student apartments, and more.
The flexible production system in the equipment is mainly supported by both hardware and software systems. To enhance product compatibility and overall precision, the system incorporates high-precision flexible fixtures at the hardware level. Utilizing a multi-axis adjustable mechanical structure, the system intelligently adapts to different product specifications, providing multi-point high-precision clamping and positioning capabilities.
At the software level, the system utilizes Roboticplus.AI self-developed RobimWeld software, equipped with a user-friendly human-machine interface. By reading drawings or model information, the software provides offline simulation and simulation functions, generating robot laser vision positioning and welding paths automatically. Moreover, it can adjust welding procedures and parameters based on product dimensions, enabling multi-robot collaborative fully automated welding. This software streamlines the welding process, enhances efficiency, and ensures precise and consistent welding results.
Compared to traditional automation solutions with limited workpiece compatibility and long changeover times, GrandRealm's flexible production system, supported by the aforementioned hardware and software, maximizes compatibility with different product types. The integration of RobimWeld software enables one-click changeover, facilitating seamless digital integration between design and construction. This approach allows for diversified designs while meeting the demands of large-scale automated production.
Currently, the MiC intelligent welding production line is continuously operating on-site, providing ongoing value to customers through its flexible and intelligent features. In practice, it has brought several improvements to the factory, including:
1.Overall welding efficiency improvement
Exactly! The automated welding production line achieves high-speed and continuous welding operations, significantly reducing welding cycles and production time. Compared to traditional manual welding, automated welding can rapidly complete large batches of welding tasks, enhancing production line capacity and efficiency. This improvement in productivity not only increases output but also ensures consistent and high-quality welds, making it an essential component of modern manufacturing processes in various industries, including the modular integrated construction sector.
2.More Stable Welding Quality
Automated welding production lines achieve a high level of welding process stability through precise control and monitoring capabilities. They enable precise control of welding parameters and welding speed, ensuring the consistency and quality of weld seams. Moreover, they reduce the impact of human factors on welding quality, enhancing welding consistency and repeatability, thereby ensuring the quality and performance of the products.
3.Safer Production Process
Automated welding production lines contribute to a safer working environment by reducing direct contact between workers and welding equipment, thereby lowering potential safety risks and the likelihood of accidents. These production lines are equipped with various safety measures, such as emergency shutdown devices and fire alarm systems. During the production process, workers can monitor equipment status from a safe area, ensuring safety and protection throughout the welding process.
4.Reduction in Overall Welding Production Costs
This production line adopts a dual-machine, multi-axis collaborative approach, effectively shortening welding time, reducing manual operations, and lowering labor costs, thereby increasing production efficiency and capacity utilization. The RobimWeld automated welding system can automatically adjust welding strategies based on product types, optimizing the usage of welding materials, reducing waste, and cutting costs significantly.
Conclusion
Roboticplus.AI will continue to focus on the modular integrated construction industry, leveraging its research and development capabilities and accumulated expertise. By fully utilizing its comprehensive advantages in intelligent construction, Roboticplus.AI aims to promote the sustainable, healthy, and high-quality development of the modular integrated construction sector, including prefabricated and assembled buildings.