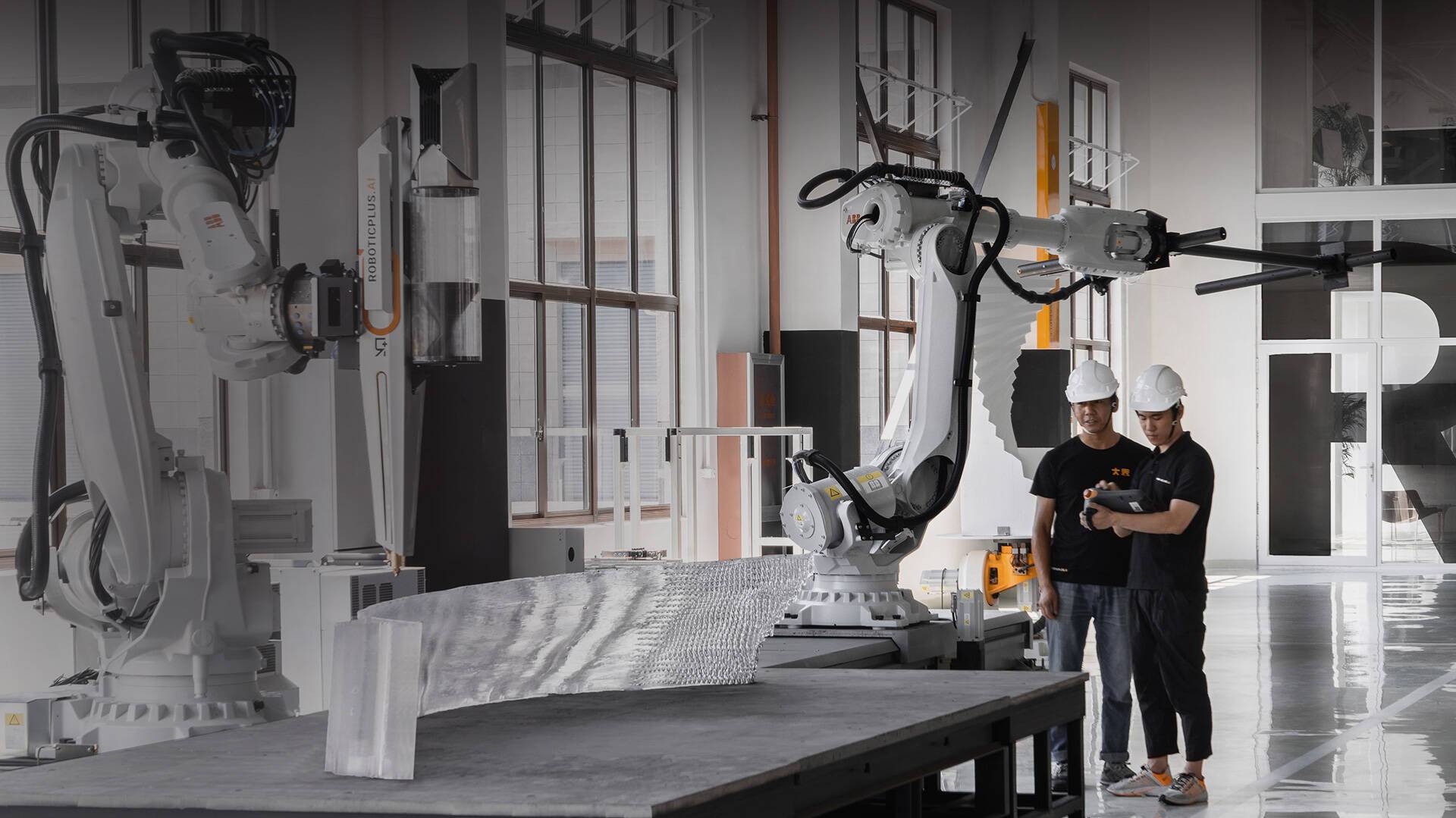
News
cutting-edge technology
1. Industry development status
With the continuous development of China's manufacturing industry, the application of welding has penetrated into various fields of industrial production, but the welding site environment is harsh, smoke, arc, metal splash seriously hurt the health of workers, while workers also need a long time of training and experience accumulation, in order to meet the production process requirements. Therefore, fewer and fewer young people are engaged in welding work, and the industry is generally facing the problem of difficult recruitment, expensive labor, and high threshold.
In this context, the new welding mode represented by welding robots is breaking the multiple restrictions brought by traditional manual welding such as cost, environment, work intensity and professional requirements. However, in the face of the multi-variety and small-batch production needs of the discrete manufacturing industry, welding robots are still faced with intelligent and flexible problems in the actual production process. To really get the solution path, we need to briefly review the development of robots in the field of welding and understand the principles and limitations behind it.
2. Current situation and future of welding robot
Stage 1: Teaching welding robot
Before the operation, the worker should guide the robot to perform the entire welding process in advance, and the robot records the action instructions in the process, including welding position, attitude and parameters, etc. After the worker completes the teaching, the robot repeats the content taught and completes the welding task.
Advantages
No environmental model is required, suitable for batch operation scenarios with simple workpiece configuration and high repeatability, such as 3C, automotive and other industries.
Disadvantage
The scene Self-Adaptation ability is poor, and it takes up production time when teaching the robot. For example, if the position shift occurs during operation, or the product configuration is adjusted, the current production task of the robot must be interrupted, and it must be re-taught before running. The whole process is cumbersome and inefficient, so the consistency between the assembly quality and accuracy of the workpiece is required to be high, and the system tolerance rate is low.
Stage 2: Offline programming of welding robots
It is only necessary to set the welding gun angle, speed, trajectory, etc. in an all-round way through a specific offline programming software in the computer, and generate the robot running code to complete the job. At the same time, it is necessary to independently set the fixed welding current, voltage and other processes on the welding machine. For some software with simulation modules, the robot path can be simulated before actual welding, and manual adjustment can be made to ensure that the processing path is correct and collision-free.
Advantages
Compared with the traditional teaching programming, the robot can be programmed on the computer without stopping or leaving the production line, and the efficiency is greatly improved.
Disadvantage
For more complex workpieces, the establishment of weld paths, trajectory and process planning in offline programming are still very tedious, which can adapt to large-scale, batch and standardized production scenarios, but cannot meet the industry needs of small batches and multiple varieties. In addition, if the relevant parameters of the welding machine are adjusted during the production process, the operation needs to be interrupted and the required data needs to be input by the buttons and on the manually operated welding machine, so it is not suitable for production scenarios that require frequent switching of welding processes.
Stage 3: Welding robot based on workpiece feature template
Compared with the previous two stages, the welding robot in this stage has certain flexibility and can make Self-Adaptation adjustments to more complex production processes within the set range. By manually abstracting and summarizing the structure and process types of the product, the corresponding feature template classes are established in the software, and these feature templates are mapped with the set parameters one by one in actual production to be converted into specific template examples. For specific welding scenarios, it is only necessary to manually quickly judge and select the correct template type, and assign the parameters in the template one by one to complete the setting of different welding components and processes.
Advantages
Through the establishment of feature templates, the robot trajectory, welding process and high efficiency can be quickly matched, which can meet certain flexible production scenarios.
Disadvantage
In the face of enterprises with large production volume, it is necessary to manually select the corresponding feature template, which will still occupy a lot of time, resulting in the extension of the engineering cycle, and once the target feature is not in the template library or exceeds the feature range, the robot cannot handle it, and it is necessary to re-establish a new feature template, which affects the continuity of production and labor costs. In addition, the characteristic template is extremely susceptible to environmental interference or constraints. Any changes in template parameters, such as the machining and assembly accuracy of components, the angle, size, weld position, orientation, the process used, the position and distance of adjacent parts, and even the previous The position and length of the positioning weld in the process may challenge the original template setting. Once the environmental change does not match the original template setting, it will trigger a chain reaction and lead to the overall failure of the template. In the end, a large number of production and debugging work cannot be separated from human intervention and processing.
Through extensive research and exchanges with customers and experts in the industry, RoboticPlus.AI believes that the next stage of welding robots is:
Flexible intelligent welding robot with autonomous decision-making ability
Compared with the previous three stages, the welding robots in this stage have undergone multiple evolutions in the field of "hand-eye-brain", completely getting rid of the robot's dependence on artificial labor. Use software to replace the human brain for autonomous learning and judgment, use high-perception visual sensors to replace the human eye for precise positioning, and dispatch the robotic arm to achieve stable obstacle avoidance and high-quality welding, so as to achieve the true meaning of "bid farewell to the tedious operation of software and enter the era of one-click welding" to help customers achieve the purpose of reducing costs, increasing efficiency and improving quality.
In terms of efficiency, one workstation can coordinate multiple robots, replace several skilled welders, and perform welding operations 24 hours a day, greatly reducing labor costs and improving overall production efficiency. At the same time, powerful software functions can greatly reduce the process drawing cycle and processing cycle of the project, and workers can be freed from the tedious software programming and setting work, and can manage multiple workstations at the same time to maximize per capita production capacity. In addition, its high degree of flexibility can cover a wider range of processing component types, realizing the transformation from "special plane" to "flexible machining center", helping enterprises reduce equipment investment and obtain higher input-output ratio.
Based on this, RoboticPlus.AI launched the RobimWeld intelligent welding system.
3.Roboticplus.AI RobimWeld core technology advantages
1. Software platform for hand-eye-brain collaboration
The RobimWeld intelligent welding system developed by Roboticplus.AI is equipped with cutting-edge geometric algorithms, visual algorithms, robot motion control algorithms and other technologies. It can quickly read two-dimensional drawings or three-dimensional models of steel structure components, and locate and correct them through different types of visual sensors. Correction, can quickly calculate the position of the workpiece weld, and automatically generate accurate welding paths and motion attitudes. Using the data format and interface parameters that match the welding robot, the welding process parameters can be automatically recalled, modified, stored and optimized, and the robot welding program can be generated in the shortest time and easiest operation to realize intelligent welding of various types of welds in steel structures.
RobimWeld Software
For robot welding scenarios, Roboticplus.AI builds a multi-dimensional composite data standard system from the bottom to ensure the uniformity and effectiveness of different data sources and interfaces. When the production process and component types change, the software platform can help enterprises achieve seamless Adjust and switch, and support long-term production line expansion and upgrade. At the same time, after a lot of user research, the software is equipped with an open and friendly interactive interface, combined with customized production scenario solutions, without any software and robot expertise, field operators can be familiar with the entire system in a very short time. Use and operation, rapid production.
While improving the productivity of operators in the workshop, RobimWeld can also become an efficiency tool for deepening, drawing and craftsmen. Functions such as one-click generation of welds and one-click process matching can greatly save the drawing and checking of dimensioning, process marking and node views in traditional processes, and shorten the design deepening and delivery cycle of projects. The production management module of the software can realize the rapid scheduling and scheduling of projects and projects, and also allow managers to conduct real-time equipment monitoring and production capacity monitoring for each workstation, and quickly adjust and assign tasks to achieve from scheduling to blanking. The optimal solution to production.
2. Geometric algorithm
RobimWeld software is embedded with powerful geometric algorithms, which can automatically parse plane or three-dimensional model geometric data, extract key feature information based on model or visual point cloud data, automatically identify and classify parts, and parse detailed geometric data to generate welding technology. key data. At the same time, the geometry module of the software can uniformly process large quantities of data, and transfer the components that used to require manual drawing and programming one by one to the software in the form of project packages for fast and independent processing, which can complete the daily workload of the technician in a few minutes, saving a lot of time cost.
One-click generation of model weld
In addition, the geometric algorithm can automatically align the components to the workstation, automatically calculate the center of gravity of the components, the clamping position of the fixtures, etc., to fully avoid displacement or overturning during the movement of the components, causing safety accidents or interfering with the transportation and conveying devices, and ensure that there is no temporary interference in the production process. Adjustment leads to job interruption.
3. Vision algorithms
RobimWeld is equipped with a vision algorithm built by the Roboticplus.AI Foresight algorithm team over the years, and is compatible with various types and brands of vision sensors to meet the scenarios of component positioning, part positioning, and high-precision weld seam positioning during the welding process. For example, in the process of coarse positioning of components, the algorithm can be combined with visual sensors to take pictures of 2-4 key features according to local cloud point features, and quickly solve the placement position and direction of components, saving the time spent on global multi-position photography. For large-sized components, the coarse positioning time can be shortened by 80%.
Accurate model point cloud and weld feature extraction
In the process of precise positioning of the weld, the entire weld or part can be quickly visually scanned and reconstructed, the position of the weld can be accurately analyzed, and potential deviations in the design and assembly process can be handled independently. At the same time, the algorithm includes accurate identification of welded holes, wrapping angle identification and other functions, combined with the geometric characteristics of the workpiece for accurate arcing and closing control to ensure the welding quality to the greatest extent. Combined with Deep learning technology, the algorithm improves the stability of the overall visual system while realizing millisecond-level weld seam positioning, and helps customers easily cope with the limited welding accuracy and quality caused by harsh environments such as ambient light, arc light, and smoke during operation.
4. Robot motion control algorithm
Roboticplus.AI robot motion control algorithm has the functions of collision detection and intelligent trajectory planning, which can take into account technology, efficiency and safety in all aspects. In the face of complex welding tasks, it can quickly identify the positional relationship between the robot body, components and the environment, avoid the occurrence of actual welding robot collisions, limits, singularities, etc. At the same time, the processing trajectory and welding process attitude are intelligently planned, saving manual debugging costs and improving the operating efficiency of the robot.
Multi-arm complex trajectory planning
In addition, the algorithm can independently assign tasks to two or more robots and cooperate with each other without interference, realizing complex trajectory planning for multiple robots. For component welding with assembly deviations, compensation data can be obtained based on deviation statistics, and the robot trajectory can be corrected in real time to ensure the best welding quality under any working conditions. In order to better plan and evaluate the production process, efficiency and beat on site, RobimWeld is equipped with an easy-to-use simulation module, which can dynamically simulate the attitude and trajectory data generated by the algorithm, allowing users to intuitively see the real and accurate processing trajectory preview
5. Intelligent welding process expert library
The Roboticplus.AI intelligent welding process expert library covers common welding application types, including welding materials, shielding gases, welding joint forms, basic shape and size of welds, weld space attitude, etc. Combined with the intelligent data decision-making system, this process expert library can give the most suitable welding process configuration based on known data information, such as current and voltage, welding speed, welding gun angle, swing frequency, gun operation method, arc starting and closing and joint parameters, etc. For the multi-layer multi-pass welding of medium and heavy plates, the corresponding parameters and process trajectories of different weld beads and layers can be quickly generated based on data such as groove form, assembly gap and weld posture. In this process, there is no need to manually set and edit each weld or even each weld independently, which improves efficiency as a whole while ensuring the welding quality, stability and consistency.
Weld type
At the same time, in order to quickly respond to changes in the environment caused by uncontrollable factors, such as temperature, humidity, cleanliness of welding materials, etc., the Great World Intelligent Welding Process Expert Library supports users to customize and edit the process database, and for users who have applied robot welding, It can support the direct import of existing process parameters, and on this basis, combined with the actual welding process test and evaluation results, process optimization and iteration are carried out.
4. Welding application scenarios based on RobimWeld
1. Section steel welding
RobimWeld intelligent steel welding center is mainly composed of welding robots, vision systems, suspended guides and positioners. It can weld various simple or complex steel components, and quickly identify rib plates, end plates, ox legs and unconventional node types. The software can realize millisecond-level weld generation and process matching. For complex workpieces, hundreds of welds can be automatically generated within seconds. Users can choose line laser or 3D structured light vision sensor according to their needs. After visual recognition, the welding accuracy can reach ± 0.5mm. With the robot welding arc tracking, the accuracy and quality of the weld can be ensured to the greatest extent. At the same time, the positioner system can freely flip the components 360 degrees. With the trajectory planning and intelligent process matching functions of the software, it can realize one-click component flipping, and transform the vertical weld seam into a fast operation of flat weld welding, which can shorten the operation. Time while improving welding speed and weld quality.
The workstation can meet the welding of components in the range of 2-18m in length. After the on-site operator loads the material and introduces the processing model, the whole process does not require manual intervention, and the multi-sided welding of section steel components is completed at one time, which can effectively save more than 80% of the on-site equipment. Debugging and operation time, in the unit time, the welding arcing time is increased to the traditional 200%.
2. Bridge baffle welding
RobimWeld intelligent baffle welding center can meet the welding scenarios of bridge baffle and ship group. The system consists of two welding robots, gantry guide rail and vision system, and has the function of automatic workpiece positioning. Workers can place the workpiece at any position and angle of the welding platform. After a wide range of visual scanning and recognition, it is automatically matched with drawings or models in the component library to achieve fast and accurate component and weld seam positioning. The workstation can effectively identify common complex node forms in baffle and group setting scenarios, such as hole ring stiffening and oblique edge stiffening, and can independently allocate the welding processes required for corresponding nodes, such as flat angle welding, interchange welding and different forms of Wrapped angle welding, etc. At the same time, the software supports automatic processing of unconventional node forms brought about by various node combinations, so that the product processing range can cover more than 98% of bridge baffle components and more than 95% of ship group standing components.
In addition, it supports multi-machine collaborative welding and automatic welding task assignment. By accurately controlling the speed, position and arcing beat of the two robots, the collaborative welding of the weld seam on the opposite side of the stiffening plate is completed, effectively reducing welding deformation. The simulation function provided by RobimWeld software can help operators quickly preview the complete welding process of the subsequent workpieces to be welded while the workpiece is welded, greatly reducing the time loss caused by node or process modification. The simple and intuitive operation interface and process, combined with all-weather non-stop welding, can increase the production capacity of this scenario to 150% of similar workstations.
5. RobimWeld+RobimCut
In most steel structure production enterprises, welding and cutting is the most important process, and runs through the entire production process. However, due to the complexity of materials, processes and processes, the software systems between welding and cutting equipment are independent. The project information, product data and task flow at the end cannot be opened up, which greatly affects the production efficiency of the enterprise.
To this end,Roboticplus.AI has built a multi-dimensional composite data standard system based on steel structure scenarios to realize the interconnection and interoperability of RobimWeld and RobimCut intelligent cutting systems and workstations. After disassembling the model data according to different component types, the processing tasks are assigned to the corresponding equipment in the production workshop, and the loading and unloading of parts, groove cutting, logistics transportation and integrated forming welding are automatically completed. At the same time, driven by data, the software can comprehensively monitor the production progress, equipment operation status, process parameters, product quality, etc. of each key station, forming an integrated solution of "design-process-equipment-control", reducing data loss in the production process, ensuring that the data in the processing process can be monitored, traced and counted, and improving the overall production efficiency of the workshop. In addition, the software can seamlessly connect to MES, ERP, WMS and other systems, realize the data closed loop of the whole process of production management and enterprise management, and help the digitization and intelligence of steel structure production enterprises.