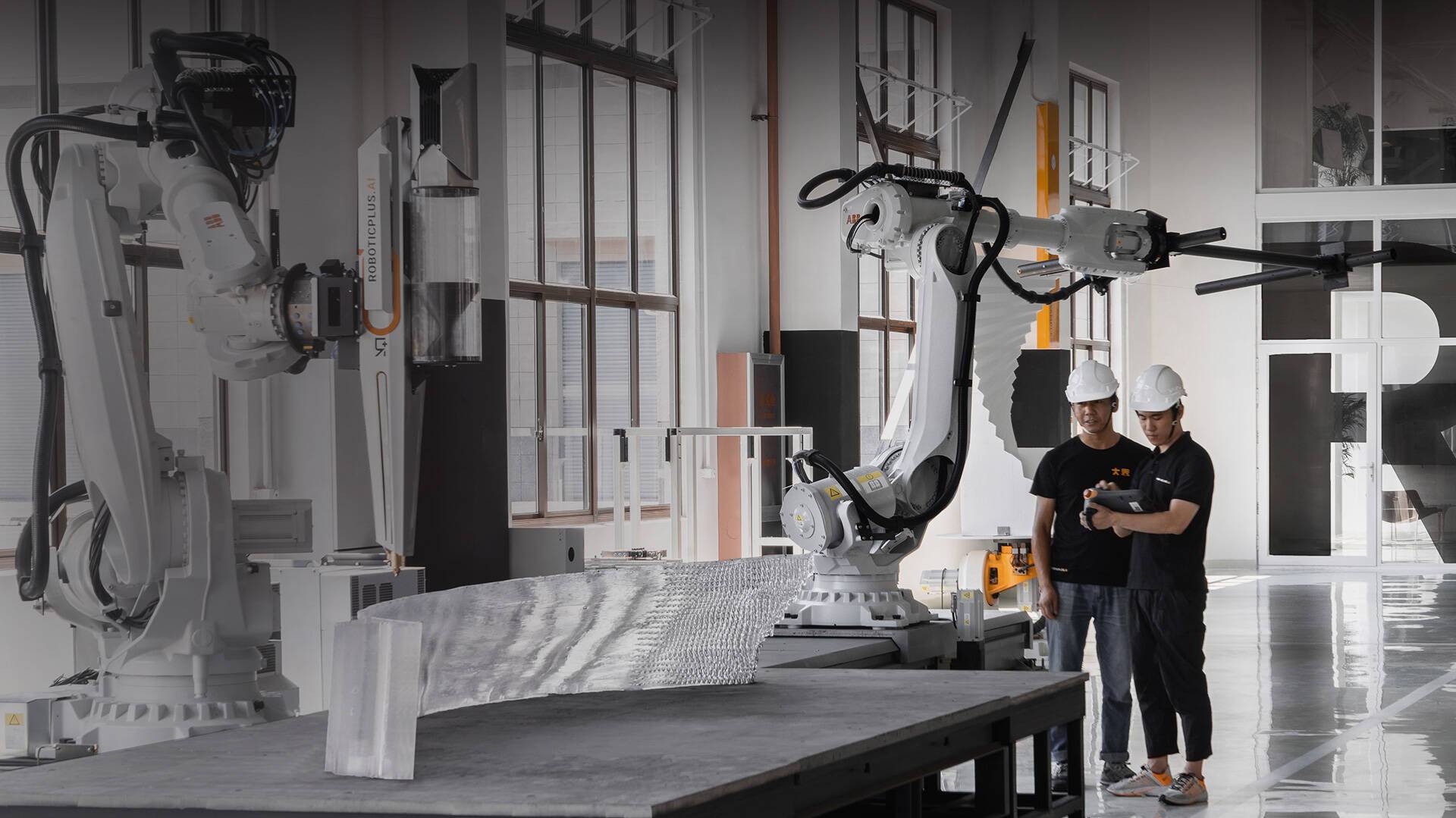
News
cutting-edge technology
RoboticPlus.AI provides medium and thick plate plasma bevelling robot solution for a head coal machine manufacturing enterprise.
For the cutting scene of hydraulic support parts, RoboticPlus.AI through self-developed industrial software RoBIM, combined with
advanced visual algorithms, to help customers solve the problem of large deviation of workpiece, difficult positioning of tooling,
low efficiency of manual teaching, and strong dependence on process experience.
1 Project pain point
1.Workpiece sizes and specifications are varied
The size and type of the workpiece of the hydraulic support are varied, and 100-500 kinds of different specifications of the groove workpiece need to be
processed.
2.Manual teaching is cumbersome
Traditional manual teaching, tooling needs extra time to insert and remove the limit pin, the operation is cumbersome, highly dependent on skilled operators,
high process requirements, teaching accuracy is difficult to control, low efficiency.
3.Workpiece positioning is time-consuming and labor-intensive
4.Large deviation of incoming materials
The workpiece discharge is dense, the blanking is prone to defects and deviations, and the repeated cutting of a single procedure leads to the accumulation of
processing errors,which affects the subsequent welding quality.
5.Extra long workpieces are limited
The length of ultra-long workpieces is more than 4 meters, and the existing workstations for processing ultra-long workpieces are limited, mainly relying on
manual cutting,and only 1-2 teaching cutting stations can process ultra-long workpieces.
2 solution
1.Import drawings in batches to quickly generate groove parameters
After importing drawings in batches in RoBIM, the groove parameter setting can be completed in 20 seconds, the three-dimensional model can be automatically
generated,and the process of marking each workpiece in the two-dimensional software can be simplified, so as to meet the centralized editing, visual viewing and
unified production.
Groove parameter one key edit
2. Multi-workstation configuration to match different production modes
For the production mode of hydraulic support parts with few batches and many batches, the robot alternates between the two workstations,
and the personnel loading and unloading and the robot cutting are seamlessly connected, greatly improving the production efficiency.
Double station multi-workpiece automatic cutting
Extra long workpiece cutting station
Customized solutions for ultra-long workpieces, which maintain high quality and accuracy while machining large-scale workpieces, can
meet the specifications of 8-10 meters of hydraulic support for the processing of ultra-long workpieces.
Automatic cutting of long workpieces
3.The workpiece position is placed at will, easy and convenient loading and unloading
RoBIM software is embedded with a self-developed visual algorithm, which can locate the position and position of the workpiece,
save the time of loading and inserting and removing the limit pin, and automatically identify and process the workpiece without
straightening, making the loading and unloading operation easier and more convenient.
Easy manual feeding
Visual system coarse positioning of the workpiece
4.Intelligent algorithm assists incoming material reconstruction to achieve high-precision 3D correction
The large-boundary vision algorithm can accurately identify the deviation between the actual size of incoming materials and the drawing,
reconstruct the processing contour,correct the cutting path of the robot, and match the optimal algorithm to achieve the best cutting
effect. When the deviation exceeds the preset value, the algorithm system will provide the optimal solution strategy independently.
3.Multi-workpiece automatic processing, improves production efficiency
With advanced visual algorithms to analyze the contours of massive workpieces, automatic processing of the same batch or different
batches of multiple workpieces in a single workstation can be achieved, greatly reducing the frequency of manual loading and unloading
and reducing labor intensity.
3 Customer revenue
1.Mass workpieces, one-click cutting
In the past, complex workpieces needed to be handled manually or spent a lot of time on manual teaching, but now it is only necessary to import
the workpiece drawings according to the operation process in RoBIM to achieve one-click processing.
RoboticPlus.AI double station and ultra-long workpiece cutting station help customers in the production of high-end large mining height
hydraulic supports, the comprehensive output value of a single production cycle compared to ordinary supports increased by 3.5 times.
2.Increase production capacity by 2-4 times
Due to the wide variety of workpiece types contained in the high-end hydraulic support, the teaching and process debugging time
can be greatly saved through the large-scale vision system, and the production capacity of hundreds of small-batch workpieces can
be increased by 2-4 times.
3.Eliminate 1 teaching operator
With the RoboticPlus.AI Teaching Free system, you can get rid of the dependence on the teaching operation plant and only need to
retain ordinary loading and unloading workers. Each single station can save the labor cost of 1 skilled operator, and 1 worker can
take into account 2 workstations at the same time, cooperatively process multiple processing workpieces, and the efficiency is greatly improved.